超精密加工に単結晶ダイヤモンド工具が最適である3つの理由
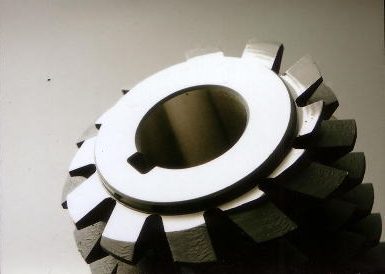
「単結晶ダイヤモンド工具=高硬度」という印象を持つ方は多いと思います。しかし、なぜ超精密加工に単結晶ダイヤモンド工具が使用されているのか、その理由をご存知でしょうか。ここでは、超精密加工に単結晶ダイヤモンド工具が使用されている理由を大きく3つに分けて説明いたします。
1.ダイヤモンド=最も硬い材質
まずはなんといっても、その高硬度という特性がダイヤモンド工具の特徴です。ダイヤモンドはモース硬度と呼ばれる硬度の指標において、最も高い10に位置しているため、その名の通り最も硬い材質と呼ぶことができます。
高硬度である特性は、微小領域において加工が行われる超精密加工においては必須の特性になります。数マイクロメートルの切込み量となる超精密加工では、工具に非常に大きな負荷が微小接点領域に発生します。この大きな負荷に耐えることができる工具材質でなければ超精密加工を行うことはできません。また一般的に、硬度が「工具>ワーク」でなければワークを加工することができないと言われております。そうでなければ、ワークによって工具が加工されてしまうためです。よって、高硬度であることは超精密加工用の工具においては必須条件となります。
しかし、ナノレベルの超精密加工に単結晶ダイヤモンド工具が使用される大きな理由は、高硬度以外の部分にあります。
2.高精度な工具刃先を形成可能
単結晶ダイヤモンド工具の大きな特徴は、高精度な工具刃先を形成することができる点です。
単結晶ダイヤモンドは、炭素の共有結合によってできたダイヤモンド構造によって構成されています。この強固な共有結合による結晶構造ゆえに、最も硬い材質とも言われます。そして、この強固な結晶性によって約50 nmという超高精度で工具刃先の輪郭精度を得ることができます。多くのダイヤモンド工具メーカーは、ナノレベルの輪郭精度を得ることができる点をセールスポイントにしていますが、それは単結晶ダイヤモンドの結晶構造および結晶性によって実現することができるのです。
3.高い熱伝導率
さらに単結晶ダイヤモンド工具の特徴として、高い熱伝導率が挙げられます。
超精密加工は、数マイクロメートルというスケールでの切込み量になりますが、加工中に発生した切削熱がこの微小切削領域に発生します。この切削熱によって、切削領域は約500℃にも達することが知られています。そのため、超精密加工では高い切削熱によって激しい工具摩耗が発生してしまいます。
しかし、単結晶ダイヤモンドは炭素原子の共有結合によって構成されているため、高い熱伝導率があるという特性があります。このため、微小領域で発生した切削熱が工具全体へと分散されやすくなり、工具摩耗を低減する効果を持っているのです。
単結晶ダイヤモンド工具の欠点
最後に、単結晶ダイヤモンド工具の欠点についてです。それは、脆くて割れやすいという「へき開性」です。
ダイヤモンド構造は高硬度である一方、へき開面と呼ばれる割れやすい結晶面を持っています。ダイヤモンドでは(111)面がへき開面にあたり、この面においてはダイヤモンドが割れやすくなっています。同様にダイヤモンド構造である単結晶シリコンも同様にへき開面を持っています。その結晶性ゆえに硬くて脆い、ガラスのような硬脆材料としてダイヤモンドは知られています。
そのため、単結晶ダイヤモンド工具を使用する際は、このへき開面を考慮して使用する必要があります。使用する刃先においてへき開面を避けるだけで、工具摩耗のスピードが大幅に軽減されます。特に単結晶ダイヤモンド工具を用いてレンズ金型の旋削加工を行う際は、レンズ形状にそって工具とワークの接点が変化するため、へき開面をさけるように工具のセッティングをするなどの工夫が必要になります。
高精密加工・超精密加工は、超精密・ナノ加工センターにお任せください!
超精密・ナノ加工センター.comを運営する株式会社木村製作所では、超精密加工に特化した「ナノ加工研究所」にて、日本屈指の超精密加工を行っております。超精密レンズ金型・マイクロレンズアレイを中心とした加工実績も多数ございます。
また当社は、チタンなどの難削材加工も得意としており、超精密とまではいかないものの寸法精度±0.001 mmが求められるベアリングやシャフトなどの機械部品に対する高精密加工に対応しております。
さらに、お客様の過剰品質の設計を防止するために、あらゆる角度からVA/VE提案をいたします。ナノレベルはマイクロレベルとは異なるノウハウが必要とされますが、どちらにも対応することができる当社だからこそ、最適な品質設計をお客様に提案することができます。
高精密加工・超精密加工にお困りの方は、超精密・ナノ加工センター.comまでお問い合わせください!