磨きレス切削加工で鏡面を得るためのポイントとは?
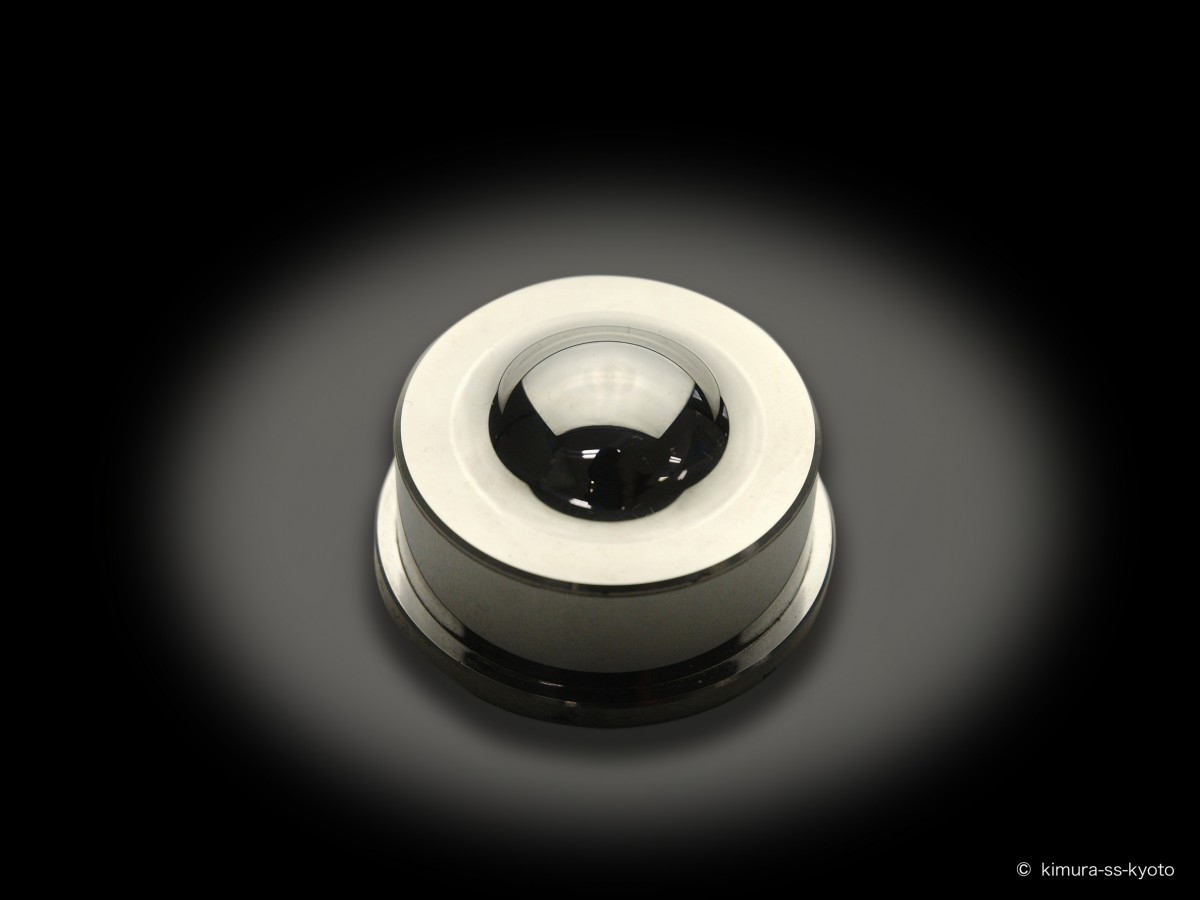
鏡のような反射のある表面を得るための鏡面加工は、一般的には研磨加工(磨き)が必須です。しかし近年は、磨き工程がないものの鏡面を得ることができる、磨きレス切削加工のニーズが一段と高まっています。
そんな磨きレス切削加工で高精度な鏡面金型を削り出しで加工するためには、超精密マシニングセンタをはじめとした特殊設備や、単結晶ダイヤモンド工具やΦ0.1クラスの小径ボールエンドミルを中心とした超精密切削用工具、さらには技術ノウハウの観点も含めて、抑えなければいけないポイントが多数存在します。
ここでは、超精密加工のプロフェッショナルである木村製作所から、磨きレス切削加工の特徴から、磨きレス切削加工の注意点、必要な設備や工具、さらには実際に当社で行った磨きレス切削加工の事例まで、まとめてご紹介いたします!
超精密加工とは?
磨きレス切削加工について解説する前に、まずは超精密加工の定義についてご説明します。
超精密加工(英:Ultra-Precision Machining)とは、最大で1/1000 μmというスケールの加工精度を達成することができる高精度な加工技術のことを指します。1000分の1 マイクロメートル=1ナノメートルとなるため、超精密加工=ナノスケールの加工精度と捉えることができます。一般的に「精密加工=マイクロスケール」とされているので、精密加工と比較してさらに一段階高精度なのが、超精密加工です。
磨きレス切削加工とは?
磨きレス切削加工(磨きレス加工、研磨レス加工)とは、超精密切削加工の一つです。超精密加工は、①超精密切削加工、②超精密研削加工、③超精密研磨加工という3つに分類されますが、磨きレス切削加工は同じ切削である超精密切削加工に該当します。
切削加工では、マシニングセンタや旋盤に取り付けた切削工具で工作物から余分な部分(加工取り代)を削り取ることにより、目的の形状や表面品質に仕上げます。この切削加工をナノスケールの精度で行い、仕上げ工程の研削や研磨を必要としないものを超精密切削加工と呼びます。
磨きレス切削加工に明確な定義はありませんが、磨きレス切削加工 = 磨きがレスな切削加工 = 研磨加工が不要なレベルまで表面性状が仕上げられた超精密切削加工、ということができます。
>>超精密研磨加工とは? ”サブナノ”の表面粗さを実現する3つのポイントをご紹介
>>鏡面加工とは?鏡面研磨との違いと鏡面加工に高い技術が必要な理由。
磨きレス切削加工のニーズが高まっている理由とは?
磨きレス切削加工のニーズが高まっている理由は、主に下記の通りです。
工程短縮
磨き工程は、職人の手作業によるものでも、工作機械を用いた自動研磨であっても、いずれにしても少しずつ磨き加工を行う必要があります。そのため切削加工後に磨き工程が入ると、非常に膨大な時間がかかってしまいます。
磨きレス切削加工では、超精密切削加工を行うため、その後の磨き工程が不要になります。もちろん切削加工は通常よりも時間がかかるようになりますが、工程が1つ短縮される方が、作業コストや位置決め精度等を考慮したとしても軍配が上がります。
複雑形状の部品や金型への加工
近年は部品の軽量化や小型化、部品点数削減という時流に合わせて、部品がどんどん複雑化しています。そのような部品に対して鏡面のような磨き精度が要求される場合もありますが、現実的に磨き加工が困難な形状の場合は、手仕上げであっても機械研磨であっても、磨き加工をすることができません。
磨きレス切削加工では、小径ボールエンドミル等の工具を使用するため、研磨では届かなかったり、そもそも対応ができない箇所に対して、磨きと同等精度の切削加工を施すことができます。特に金型や治具等の部品について、多くのお客様が磨きレス切削加工を必要とされる要因となります。
安定した継続精度(加工精度の高い再現性)
また研磨加工というのは、安定した精度で加工することが困難な加工方法です。しかし光学用金型や自動車のヘッドライト用金型、ヘッドマウントディスプレイ用金型などの部品では、複数の製品に対して同等レベルの超精密加工が求められます。それを手作業での磨き加工で実現するのは現実的ではありません。
磨きレス切削加工では、超精密工作機による加工のため、安定した継続精度で超精密切削加工を行うことができます。
これらの理由から、現在磨きレス切削加工のニーズが高まっており、実際に当社でも多くのご相談をいただいております。
磨きレス切削加工で鏡面を得るためのポイントとは?
磨きレス切削加工で鏡面を得るためのポイントは、①設備、②工具、③技術ノウハウ、の大きく3点にまとめられます。
特に工具についてですが、磨きレス切削加工のような鏡面を得るための加工では、単結晶ダイヤモンド工具が多く使用されます。実際に当社でも単結晶ダイヤモンド工具は使用しております。
しかし、単結晶ダイヤモンド工具を使用する際には、へき開性と熱化学反応に注意する必要があります。
ダイヤモンド構造は高硬度である一方、へき開面と呼ばれる割れやすい結晶面を持っています。ダイヤモンドでは(111)面がへき開面にあたり、この面においてはダイヤモンドが割れやすくなっています。同様にダイヤモンド構造である単結晶シリコンも同様にへき開面を持っています。その結晶性ゆえに硬くて脆い、ガラスのような硬脆材料としてダイヤモンドは知られています。
そのため、単結晶ダイヤモンド工具を使用する際は、このへき開面を考慮して使用する必要があります。
>>超精密加工に単結晶ダイヤモンド工具が最適である3つの理由
また、単結晶ダイヤモンド工具を用いた磨きレス切削加工を行う際は、工具摩耗を抑制するための工夫が必須と言えます。例としては、工具と金型鋼の熱化学反応を抑えるために、楕円振動切削を採用したりするケースも見受けられます。
磨きレス切削加工に必要な設備
実際に磨きレス切削加工を行うためには、ナノメートル単位での位置制御が可能な超精密加工機が必須となります。鏡面のようなナノレベルの表面粗さを得るためには、ナノメートル単位での制御が可能な工作機械でないと、工作機械の母性原理に基づいて、磨きレス切削加工は不可能になります。
当サイトを運営する木村製作所では、下記のような設備をすべて社内で保有している、国内有数の超精密部品加工メーカーです。ここでは、実際に当社が使用している設備を軸に、磨きレス切削加工に必要な設備をご紹介いたします。
超精密マシニングセンタ
木村製作所では、芝浦機械製の超精密立形加工機UVM-450D(H)を用いて、光学レンズ用金型を中心に超精密磨きレス切削加工を行っています。この超精密マシニングセンタでは、回転数60,000/min-1という超高速回転が可能となっています。
実際に当社の社員が生産現場で超精密立形加工機を使用した上で感じた特徴は、以下の通りです。
1. 機械のバックラッシュを気にすることなく、鏡面加工が可能!
2.自動工具交換装置による昼夜連続加工も可能!
3. 加工ステージ高さが低く、ワークセッティングがやり易い!
>>超精密立形加工機「UVM-450D(H)」での加工事例を紹介!
超精密旋盤
当社では、こちらの超精密非球面加工機 ULG-100D(SH3)を、自由曲面加工や光学レンズ用金型をナノ精度で旋削加工するために用いております。高い回転精度、高精度な送り駆動、ULG独自のV-Vころがり案内によって、ナノ領域の面精度が要求される超精密領域での加工を、高効率かつ高精度に実現しています。
実際に当社の社員が生産現場で超精密非球面加工機を使用した上で感じた特徴は、以下の通りです。
1.機械の絶対精度が高く、正確な追従が可能!
2.連続運用時でも累積誤差が発生しない!
3.超精密旋削やミーリング加工にも対応!
>>非球面加工機「ULG-100D(SH3)」での加工事例を紹介!
下の動画では、超精密非球面加工機 ULG-100D(SH3)の実際に動いている様子をご紹介しております。
超精密検査測定機
超精密加工に関するお話の中では、どうしても工作機械に注目されがちですが、忘れてはならないのが、測定機器です。超精密加工に超高精度な三次元測定機が必要なのは、超高精度を求められる形状に対する加工への形状誤差に対する補正の為のフィードバック、および完成形状に対する保証するためです。
超精密加工を行っている当社にとって、超高精度の三次元測定機はなくてはならない存在です。超精密加工とは、最大で1/1000 μmというスケールにおける加工精度を達成することができる加工のことを指します。1000分の1 マイクロメートル=1ナノメートルなので、ナノスケールでの加工精度が求められます。超精密加工に対応できる三次元測定機は、超精密加工機とほぼ同一精度の数値分解を持ち、他の汎用測定機では対応できない精度まで安定して測定することが出来ます。
木村製作所では、こちらの超精密非接触三次元測定機 NH-3SPを、光学レンズ用金型やマイクロレンズアレイの高精度測定に使用しております。
X及びY軸分解10nm、Z軸分解の1nmという、超高精度測定を実現しています。また半導体レーザーを用いたポイントオートフォーカス法による非接触測定のため、マイクロレンズアレイやフレネルレンズ、回折格子などの非破壊測定が可能です。
超精密加工を依頼する際には、必ず保有設備一覧を確認する必要があります。超精密加工に対応可能と謳う部品加工メーカーは多数存在しますが、①安定した継続精度で超精密加工を実現できる工作機械、②実際に超精密加工ができたかどうかを測定する設備、の2つを保有していない場合は、お客様の要求水準を満たしていない可能性があります。
磨きレス切削加工に必要な工具
磨きレス切削加工には、工作機械や測定設備だけでなく、工具や機上測定機も重要です。
小径ボールエンドミル
小径ボールエンドミルが具体的にどれくらいの径以下のボールエンドミルかという具体的な定義はございませんが、Φ1mm程度は小径と呼ばれることが多くなります。小径ボールエンドミルは、自由曲面加工や微細溝加工、部分的な超精密加工等に使用されます。
機上測定機
また小径ボールエンドミルを使用するためには、小径ボールエンドミルの振れを抑える必要がありますが、その振れを測定する必要もあります。当社では、機上測定機を保有しており、Φ0.1~0.4クラスの小径ボールエンドミルも振れを抑えた状態で使用することができます。
こちらの動画もぜひご覧ください!
木村製作所だからこそ可能な磨きレス切削加工
当サイトを運営する木村製作所では、独自の磨きレス切削加工を行っております。木村製作所だからこそ可能な磨きレス切削加工の強みは、下記の通りです。
1.光学部品専用CAD/CAM
2.超精密サブナノ研磨加工
3.最適な超精密加工方法の提案力
光学部品専用CAD/CAM
当社では、2019年度より新たに光学部品専用CAD/CAMを導入しました。これにより、日本屈指のレベルで光学部品加工用のプログラムを作成することができるようになりました。この非球面レンズ加工用のプログラムを用いて、超精密加工機を動かすことで、非球面レンズ金型の超精密加工が実現できます。
超精密サブナノ研磨加工
磨きレス切削加工とはいうものの、物によっては研磨加工が必要にもなります。そして木村製作所では、磨きレス切削加工のような超精密切削加工から、超精密研削加工、そして仕上げの超精密サブナノ研磨加工にも対応しております。
最適な超精密加工方法の提案力
上記の点を踏まえて、超精密加工全般に対応できる木村製作所だからこそ、最適な超精密加工の方法をご提案することができる、という点が当社の特徴だと考えております。
磨きレス切削加工の事例紹介
それでは最後に、当サイトを運営する木村製作所が実際に行った磨きレス切削加工の事例をご紹介いたします。
※サイトには掲載できない事例の方が多くなっていますので、予めご了承ください。
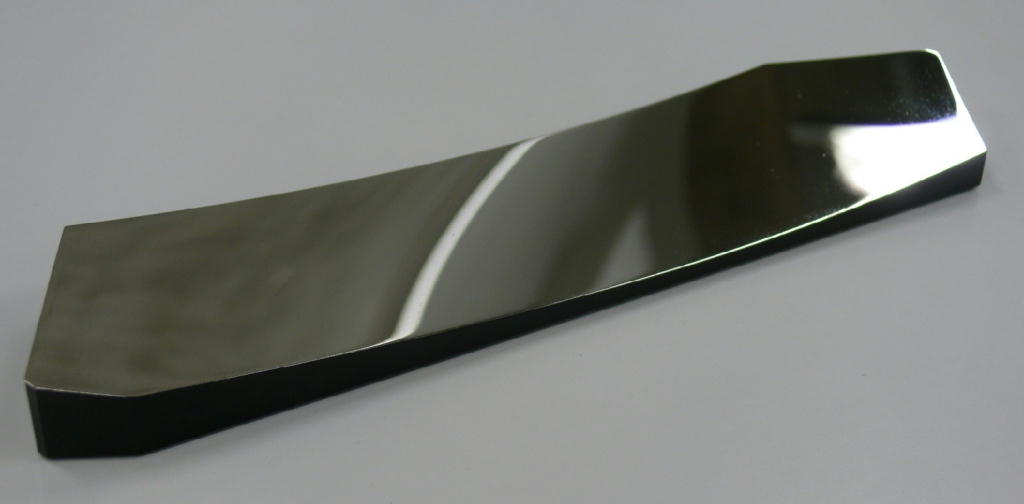
ヘッドアップディスプレイ用 反射ミラー金型
こちらは、自動車で用いられるヘッドアップディスプレイ(Head-Up Display:HUD)のミラーを成型するための金型です。光学部品専用のCAD/CAMソフトと、ナノレベルでの加工を実現する超精密加工機によって、このヘッドアップディスプレイ用反射ミラー金型の製作が可能になりました。
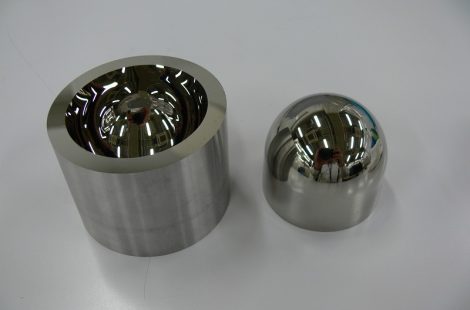
ドームレンズ成型用金型
こちらは、防犯カメラのカバーを成形するために用いられる超精密金型です。ドームレンズを成形するために、大きな凹凸を伴った形状となっています。
ドーム型形状の加工もナノレベル面精度で仕上げることができました。さらに、切削のみでナノレベルの面精度を出すことで、磨き工程を省略することができます。これが金型の全加工工程における加工時間の短縮につながり、結果としてお客様にコストダウンの提案につながりました。
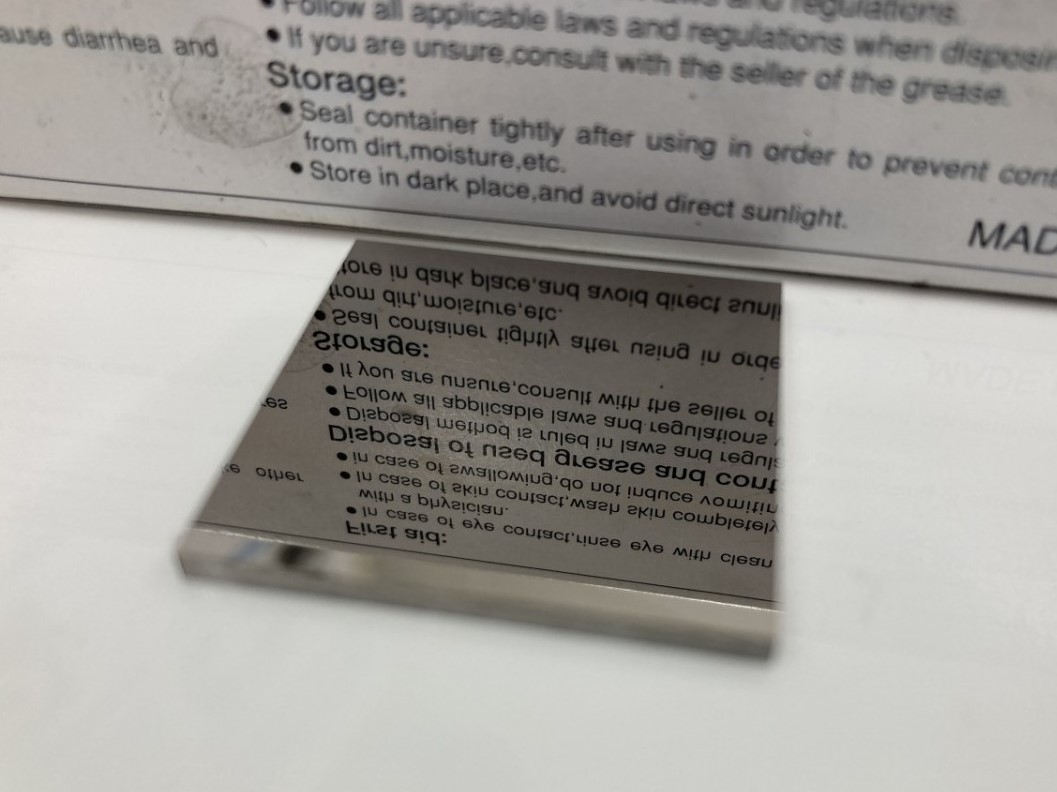
平面ミラー
こちらは、東芝機械製の超精密非球面加工機ULG-100D(SH3)を用いて超精密切削・研削加工を行った鏡面ミラーになります。STAVAX製のワークに無電解NiPめっきを施しました。
この鏡面ミラーの表面粗度はRa0.02μm。写真をご覧いただくと分かる通り、文字が綺麗に反射しており、表面粗度が非常に緻密であることが窺えます。
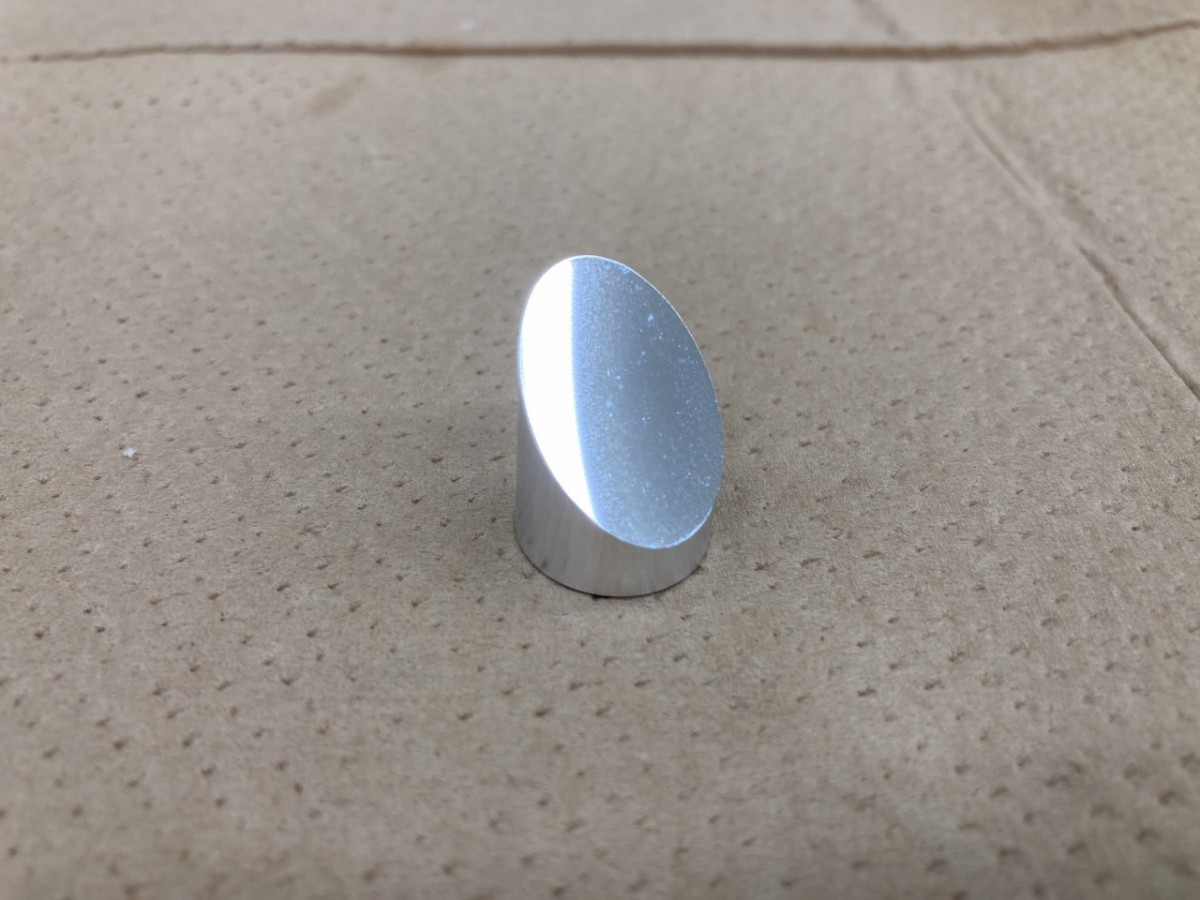
放物面ミラー
こちらは、超精密非球面加工機 ULG-100D(SH3)を用いて加工した超々ジュラルミン製の放物面ミラーです。サイズはΦ15mm×20mmになります。
半導体業界において、放物面ミラーはレーザーの散乱を減らし集光能力を上げる目的で使用されるのが一般的で、集光能力向上のためには高い精度が求められます。そこで木村製作所は超精密非球面加工機 ULG-100D(SH3)を用いてこれを加工、表面粗度Ra20nmという極めて高い精度を実現しました。
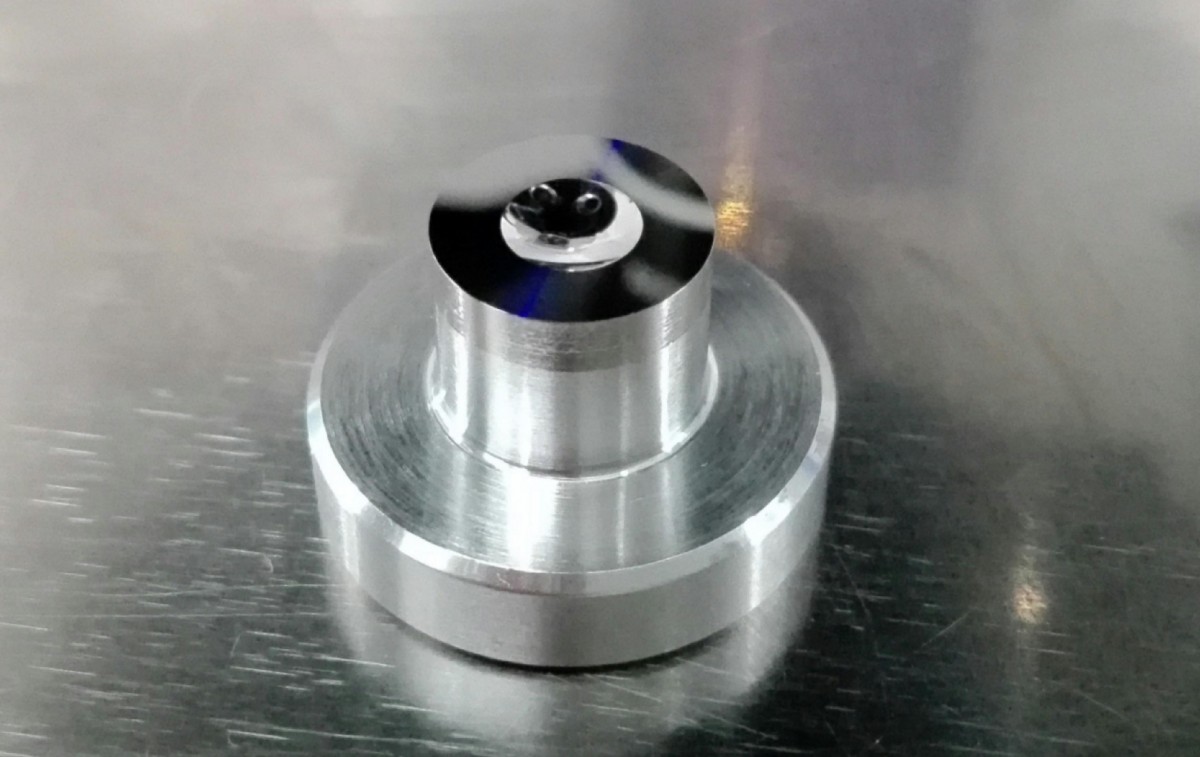
プラスチックモールド用非球面金型
こちらは、プラスチックを成形するために用いられる超精密非球面金型です。単結晶ダイヤモンド工具を用いた超精密切削加工によって仕上げ加工を行い、PV値は最大で約0.05μm、表面粗さは約3.0 nmRaと、高精度加工とナノレベルの表面粗さを実現いたしました。表面は虹面のない鏡面となり、ガラスモールド用の金型として使用できる加工面を達成しております。
磨きレス切削加工のことなら、超精密・ナノ加工センターにお任せください
超精密・ナノ加工センター.comを運営する木村製作所では、ナノレベル・サブナノレベルの精度が必要な超精密レンズ金型やマイクロレンズアレイ、自由曲面ミラーなどの加工実績が多数ございます。
部品の設計段階からのVA/VE提案にも対応しているため、お客様のご要望に合わせたコストダウン提案も可能です。ナノレベル・サブナノレベルはマイクロレベルとは異なるノウハウが要求されますが、いずれの領域も得意とする当社だからこそ、最適な品質設計をお客様に提案することができます。
「この素材の加工なんてできるのかな?」「この部分だけ精度が厳しいんだけど大丈夫?」といった案件は、超精密・ナノ加工センターにお任せください!まずはお気軽にご相談ください!